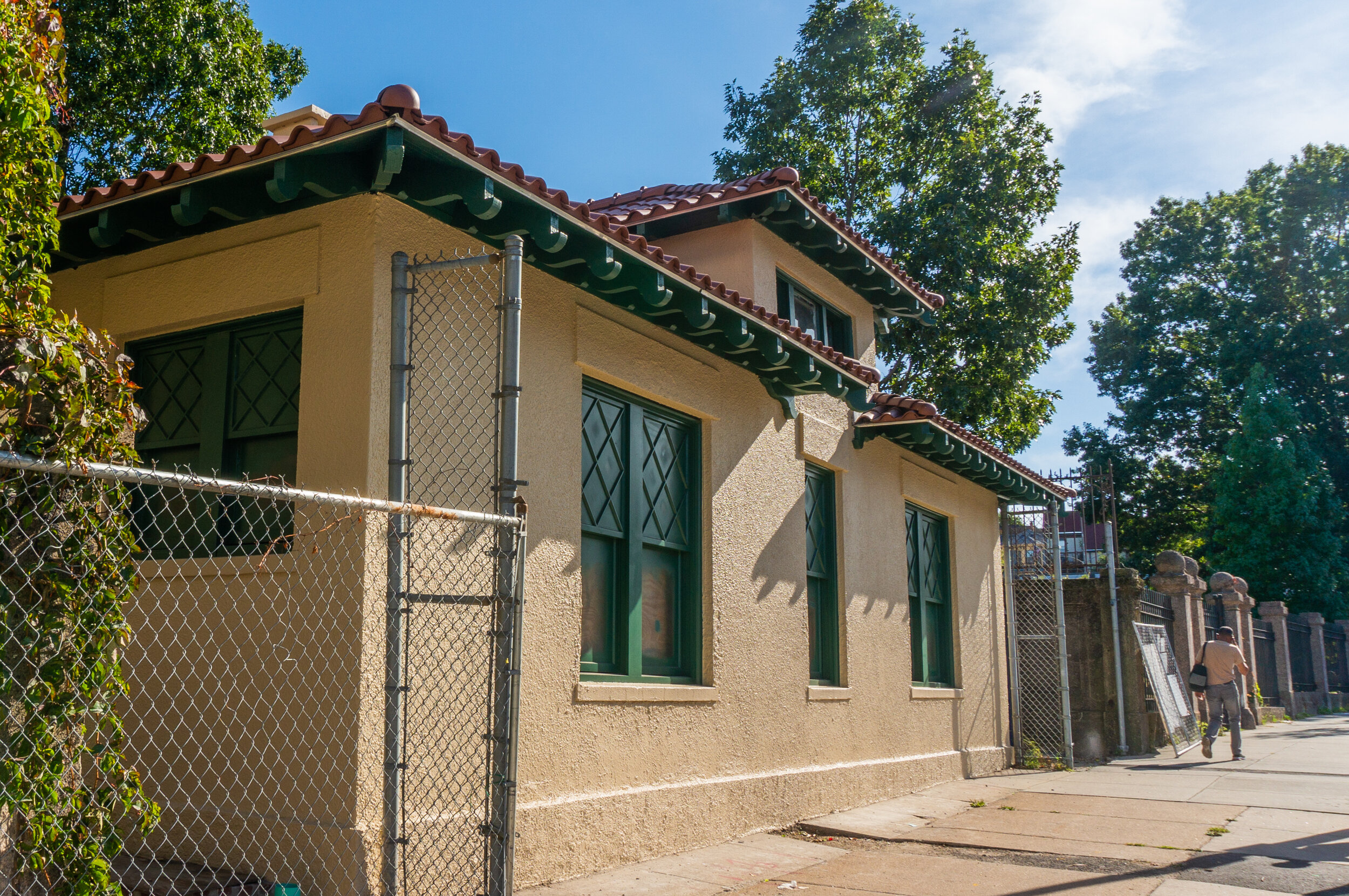
25 Mar Insulating for preservation, energy and Comfort Kitchen
Those who work in historic preservation frequently make the case that rehabilitating an existing building is more environmentally responsible than building new. While some people argue that new construction is more energy efficient, preservationists can reasonably counter that double or triple-paned windows and improved insulation reach high energy performance levels. Further, the preservationist’s case argue that the embodied energy that went into building an existing structure in the first place should not be wasted and demolition debris carted off to a landfill. Many new windows installed in new buildings today are not built to last as long as historic windows, whose efficiency increases when combined with storm windows. There will likely continue to be a tension between preservation and new construction goals, but for Historic Boston, we are committed to working with existing buildings and original fabric as much as possible and ensuring they perform to modern standards.
One of the questions that arises on each of HBI’s preservation projects is how best to insulate a building to achieve the highest R-value or thermal resistance and minimize air infiltration. Most of our projects are funded in part with State and Federal Historic Rehabilitation Tax Credits and are reviewed by both the Massachusetts Historical Commission and the National Park Service, both of which must approve proposed construction methods for the work to qualify for tax credits. Almost always, if spray foam insulation is proposed, it will be rejected because the foam adheres to historic materials that are important in defining a building’s historic character and original construction methods. The goal is to “do no harm” to the historic fabric, so treatments such as insulation need to be reversible. For this reason, we normally use other types of insulation, such as fiberglass batt or rock wool, but they have lower R-values and do not expand to prevent air leaking the way foam does.
At the Upham’s Corner Comfort Station, we have been approved to use spray foam insulation in some locations. The basement space that will be used for food prep and cleanup was previously unfinished, but the future workspace will need to be clean, dry, and comfortable for tenant Comfort Kitchen’s staff. The stone foundation walls have been covered with heavy plastic vapor barrier sheeting before being furred out for a clean, finished wall. Closed cell foam insulation will be sprayed behind the finished wall, but will adhere to the plastic sheeting rather than sticking to the stone foundation. If water should happen to make its way through the stone (to date this has not happened), the vapor and water barrier will direct it down to a perforated perimeter drain set in a gravel bed below the slab, where it will travel on to a sump pump. Of course, we hope this will never be necessary.
The main floor kitchen and dining area has been similarly prepped for insulation. Here the exterior walls are constructed of terracotta blocks which, like the stone walls in the basement, will be protected with a plastic vapor barrier that will receive the sprayed insulation. The ceiling above the room required a different treatment for insulation. Rock wool will be packed in between ceiling joists, as it would not be feasible here to wrap the joists with plastic and then spray foam insulation. These insulating methods achieve our dual goals of protecting the Comfort Station’s historic fabric for future generations while providing a comfortable, functional, efficient new home for Comfort Kitchen.